There is no excuse for poor quality in manufacturing. A connected, properly trained and enabled workforce is your best defence. As Saudi Arabia’s manufacturing sector evolves, the focus must shift toward empowering frontline workers with the tools, training, and technology needed to maintain world-class quality standards, says Vijay Jaswal at IFS.
By embracing connected worker technologies and fostering a culture of innovation, manufacturers can align with Vision 2030, contributing to a diversified economy and securing a competitive edge on the global stage.
Product quality can be a make-or-break for manufacturing success, reputation, and profitability. But as the worsening skills shortage ripples throughout the industry, manufacturers face new strains to ensure frontline workers are trained correctly and equipped with the correct tools to keep standards high.
In Saudi Arabia’s rapidly evolving manufacturing landscape, maintaining high quality is not just a priority—it’s a necessity. As the Kingdom accelerates its diversification efforts under Vision 2030, a connected, properly trained, and empowered workforce is the cornerstone of achieving excellence and global competitiveness.
For manufacturers in Saudi Arabia, product quality significantly impacts market success, brand reputation, and profitability. With a highly demanding consumer base and a global market to serve, subpar quality is no longer an option. Research shows that 70% of consumers are willing to switch brands if a higher-quality alternative is available.
This underscores the importance of proactive quality management, where errors are caught early, minimising costly recalls and preserving brand trust.
Saudi Arabia’s manufacturing sector faces challenges common to many markets—skills shortages, attracting and retaining young talent, and the integration of advanced technologies. Yet, the nation’s unique demographics and Vision 2030’s commitment to developing local talent present significant opportunities.
By harnessing the knowledge of experienced workers and capturing their expertise through connected systems, manufacturers can create a resilient, future-ready workforce while reducing the reliance on imported expertise.
While automation and AI play an increasing role in manufacturing, human intelligence remains irreplaceable certainly for now. The synergy between humans and machines is critical for continuous improvement.
For instance, frontline workers equipped with tools like Poka’s connected worker platform can:
- Access visual guides and real-time training resources.
- Collaborate with colleagues to share insights and resolve quality issues.
- Document and escalate issues to management for faster resolution.
These capabilities not only improve quality control but also support the development of a skilled workforce that aligns with Saudi Arabia’s ambitions for economic diversification.
Poka’s connected worker platform provides the opportunity to learn from other workers and their manufacturing experiences. It enables manufacturers to take their best, most knowledgeable employees and capture and reuse their knowledge. They can ensure the best people are training new employees to the best possible standards—and they only have to do it once.
The results?
When frontline workers are fully trained on the most up-to-date processes and standards, they contribute to the organisation’s ability to reduce waste, optimise production efficiency, and, crucially, minimise defects. The 70:20:10 model, which puts collaborative working on top of the learning and development scale, is precisely how training and development works for frontline workers on the shop floor.
As opposed to simply telling workers to go on a course the model focuses on 70% of learning on the job, 20% of learning through colleagues and 10% via formal training programs. In Saudi Arabia, fostering such a culture of continuous learning will help manufacturers address skills gaps while enhancing productivity and quality standards.
The integration of connected worker platforms with ERP systems enables manufacturers to manage the entire quality lifecycle seamlessly. This includes:
- Monitoring supply chain performance.
- Ensuring compliance during manufacturing processes.
- Managing maintenance, warehousing, and distribution.
For example, food manufacturers in Saudi Arabia can use ERP systems to uphold rigorous food safety standards, minimising the risk of recalls and safeguarding consumer trust.
The need to ensure transparency and control across the entire manufacturing lifecycle is essential. In the food and beverage sector for example, food safety is a top priority, and it’s where an ERP system can uphold quality control standards.
Product recalls are costly and can negatively impact brand equity.
Case Study
Poka’s customer, Barry Callebaut, demonstrates the power of connected worker solutions. The company significantly improved its ability to capture and address quality issues, using visuals and media to share insights across shifts and escalate issues as needed. For Saudi manufacturers, adopting similar tools can ensure transparency, enhance productivity, and foster a culture of continuous improvement.
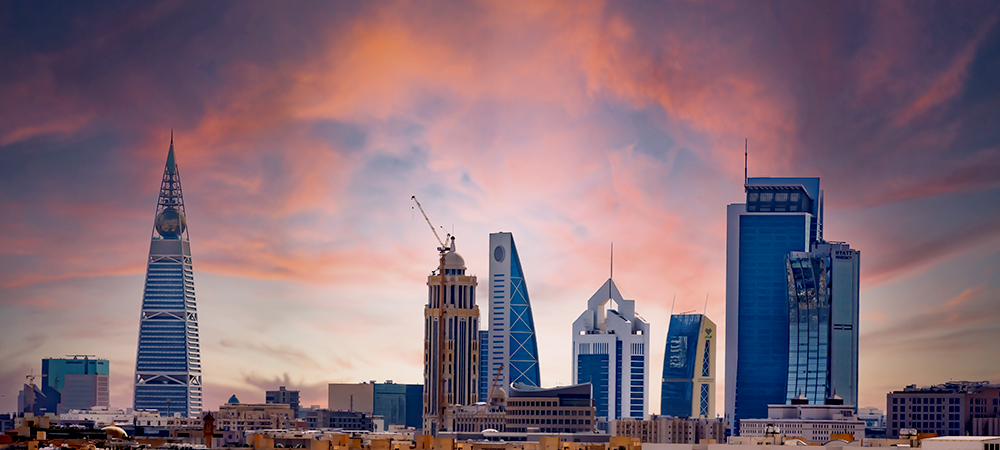